Развитие современной экономики характеризуется постоянным ростом энерго-потребления: если минимальный объем потребления энергии за всю историю человечества составляет примерно 160 млрд. т условного топлива, то из них не менее 110 млрд. т приходится на последние 35 лет.
За последние четверть века доля нефти и газа в топливном балансе увеличилась более чем в три раза.
- Транспортировка нефти и газа производится непосредственно от 1 мест их добычи по стальным магистральным трубопроводам.
В последнее время трубопроводный транспорт стали применять и для транспортировки на большие расстояния этилена и аммиака. - Ведутся интенсивные исследовательские работы с целью доставки по трубопроводам сыпучих и других материалов.
- В перспективе намечено применять не только стальные, но и пластмассовые трубопроводы.
- Основной технологический процесс при строительстве трубопроводов - сварка. Общая длина кольцевых швов при сварке трубопроводов только в 1976 г. превысила длину экватора земного шара.
![]() |
Впервые сварку трубопроводов в нашей стране применили при строительстве нефтепровода Грозный-Туапсе (1927-1929 гг.). На этом трубопроводе для соединения стыков применяли газовую и электрическую дуговую сварку, а также муфтовые резьбовые соединения.
В 1929 г. газовой сваркой был полностью сварен нефтепровод Баку- Батуми. Электродуговую сварку начали широко применять лишь в 1933- 1935 гг. при сооружении нефтепровода Гурьев -Орск. Механизированные способы сварки кольцевых швов магистральных трубопроводов начали применять в 1945-1953 гг. при строительстве трубопроводов Саратов-Москва, Дашава-Киев-Брянск-Москва и Ставрополь-Москва.
В результате исследований, проведенных ИЭС им. Е. О. Патона, удалось впервые в мировой практике использовать при сооружении магистрального трубопровода механизированную сварку под флюсом. На строительстве газопроводов в этот период применяли установки для газопрессовой сварки, приобретенные в США.
В 1952 г. на строительстве трубопровода диаметром 377 мм впервые в мировой практике была применена стыковая сварка непрерывным оплавлением передвижными агрегатами с контурными сварочными трансформаторами, разработанными ИЭС им. Е. О. Патона с участием ВНИИСТ и КФ СКВ «Газстрой-машина».
Инициатором применения при строительстве трубопроводов сварки под флюсом и стыковой сварки передвижными агрегатами был Е. О. Патон.
В освоении способов механизированной сварки большая заслуга принадлежит главному инженеру Сварочно-монтажного треста, а затем основателю и руководителю лаборатории сварки Всесоюзного научно- исследовательского института по строительству магистральных трубопроводов (ВНИИСТ) А. С. Фалькевичу.
Работы, выполненные ВНИИСТ, СКВ Газстроймашина, ИЭС им Е. О. Патона и сварочно монтажными организациями, позволили в 1959 г. применить сварку в углекислом газе и скоростными газозащитными целлюлозными электродами типа ВСЦ. В табл. 19.1 приведены данные о различных видах сварки при строительстве магистральных трубопроводов в разные периоды (в %).
До 1971 г. в СССР сооружена сеть магистральных нефтегазопроводов общей длиной около 100 тыс. км. Диаметры построенных трубопроводов не превышали 1020 мм. В связи с отдаленностью основных месторождений от промышленных центров протяженность отдельных магистральных трубопроводов достигала 3-4 тыс. км. (уникальные, например, нефтепроводы «Дружба» и Усть-Балык- Омск, газопроводы Средняя Азия- Центр и Игрим-Серов). Непрерывно возрастают диаметры трубопроводов. Если до 1952 г. применялись трубы с максимальным диаметром 530 мм, то впоследствии крупные трубопроводы сваривали в основном из труб диаметром 720, 820 и 1020 мм.
В последние 7-8 лет, в связи с открытием крупных месторождений газа в Западной Сибири и на севере европейской части СССР, строительство трубопроводов в значительной степени переместилось в северные районы страны. В настоящее время в СССР трубопроводы строят в различных климатических и почвенно-геологических условиях. В пустынных районах Средней Азии температура летом достигает +60° С, а в районах Якутии или Норильска сварочные работы выполняют зимой
1926-1935 | 1936- 1945 | 1946- 1950 | 1951-1955 | 1956-1958 | 1959 | I960 | |
Ручная газовая сварка | 90 | 20 | - | — | - | - | |
Ручная электродуговая сварка | 10 | 80 | 75 | 50 | 35 | 35 | 35 |
Газопрессовая сварка | — | — | 23 | 10 | - | - | ш I |
Механизированная сварка под флюсом | -* | 2 | 35 | 55 | 58 | 52 | |
Стыковая сварка непрерывным оплавлением | - | - | 5 | 10 | 5 | 5 | |
Сварка в углекислом газе | ш % | - | - | - | 2 | 8* | |
при температурах до -50° С, что с учетом различных составов сталей труб требует применения в каждом конкретном случае специальных сварочных материалов, особой технологии и организации сварочных работ.
Одновременно с развитием строительства трубопроводов в СССР создавались крупные заводы и специализированные цехи по производству сварных труб большого диаметра для газо- и нефте-проводов. Максимальный диаметр труб высокого давления, изготовляемых на отечественных заводах, составляет 1420 мм. Технология сварки труб на заводах разработана Институтом электросварки им. Е. О. Патона.
После 1971 г. в строительстве магистральных трубопроводов в СССР произошли значительные изменения, существо которых кратко заключается в следующем.
Диаметры наиболее мощных трубопроводов, сооружаемых на Крайнем Севере, Юге, в горных условиях возросли до 1220-1420 мм при одновременном повышении давления газа в них с 55 до 75 атм. В настоящее время для магистральных трубопроводов применяют в
основном трубы диаметром 530, 720, 1020, 1220 и 1420 мм с толщинами стенок от 7,5 до 26,0 мм.
Усложнились составы сталей труб. Эквивалент углерода
в ряде случаев возрос до 0,5.
В связи с повышением нижнего (расчетного) временного сопротивления труб до 539-588 МПа и предела текучести 412-441 МПа и необходимостью гарантировать ударную вязкость при отрицательных температурах стали применять трубы, микролегированные ванадием, ниобием, титаном, азотом. Характеристики наиболее распространенных трубных сталей, применяемых в СССР для сооружения магистральных трубопроводов, приведены в табл. 19.2.
Качество выпускаемых труб должно отвечать непрерывно возрастающим требованиям. Необходимо было улучшить прочностные и вязкие свойства металла труб за счет легирования и специальной термической обработки, повысить точность концов труб, освоить выпуск новых труб большого диаметра, в том числе с многослойной стенкой на повышенное давление для сверхмощных магистральных трубопроводов, потребовалось сооружать трубопроводы для транспорта сероводородного газа. Эти трубопроводы должны быть стойкими против коррозии под напряжением. Коррозионной активностью может обладать аммиак и некоторые сорта нефти.
Указанные изменения серьезно отразились на технико-экономических показателях технологии сварочно-монтажных работ при строительстве трубопроводов.
Значительно увеличились объемы и трудоемкость сварки; необходимо было быстро переоснастить сварочно-монтажные организации новым мощным оборудованием для сварки, термообработки и контроля. Существенно усложнилась технология сварки и контроля с введением таких новых операций, как подогрев стыков, термообработка стыков, внутренняя подварка швов, панорамное просвечивание самоходными установками для контроля швов, ультразвуковой контроль швов и т. п.
В связи с изложенным в 1974 г. были приняты специальные меры по повышению технического уровня строительства магистральных нефтепроводов и газопроводов, обеспечению большей надежности их эксплуатации. Было предусмотрено улучшение свойств труб, создание новой и усовершенствование существующей технологии сварки трубопроводов различными способами, создание новых сварочных материалов и новых средств контроля швов.
В настоящее время при строительстве трубопроводов применяют различные способы сварки, при этом с учетом сварки труб на трубных заводах на автоматическую сварку под флюсом приходится около 90% общего объема сварки. Ручную сварку применяют практически только в полевых условиях для соединения труб между собой.
Марка стали 118
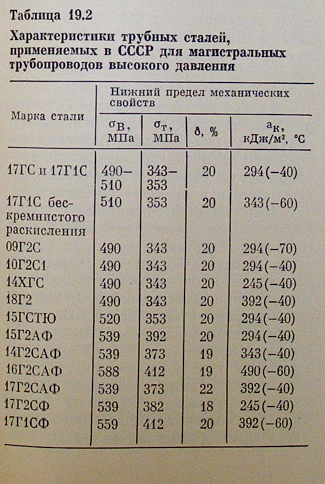
Для ускорения строительства и повышения надежности трубопроводов максимально сокращают объем сварки в полевых условиях за счет увеличения длины труб, поставляемых с трубосварочных заводов. Если 10-12 лет назад трубы имели длину б м, то в настоящее время трубы больших диаметров поставляют длиной в основном 12 м. Ведутся работы по изготовлению труб еще большей длины. Так, например, один из участков газопровода Средняя Азия- Центр построен в опытном порядке из труб диаметром 1020 мм, длиной 24 м, изготовленных Новомосковским трубным заводом. Расчеты показывают, что увеличение длины труб позволит существенно уменьшить число квалифицированных рабочих на строительстве трубопроводов и уменьшить стоимость оборудования для сборки и сварки.
Для повышения уровня механизации сварки в полевых условиях, увеличения производительности труда и улучшения качества кольцевых швов за последние годы Киевским филиалом СКВ «Газтроймашина» и ВНИИСТ разработаны специальные трубосварочные установки, на которых в полустационарных условиях осуществляют автоматическую поворотную сварку под флюсом отдельных труб и секций. Эти секции доставляют на трассу, где их сваривают в непрерывную нитку. Под флюсом в полевых условиях сваривают около половины всех стыков магистральных трубопроводов.
Автоматическую сварку на трубосварочных базах будут применять и в дальнейшем, пока трубная промышленность не начнет выпускать трубы длиной 24 м, доставляемые на трассу железнодорожным транспортом.
Современные полу-стационарные базы предназначены для обслуживания строящихся трубопроводов, как правило, при доставке труб на расстояние от 15 до 100 км. В отличие от практики США и стран Западной Европы, где сваривают секции длиной 24 м из двух труб, в СССР на таких базах чаще всего сваривают секции длиной 36 м из трех труб. В большинстве случаев перевозить такие секции нетрудно, особенно в пустынных районах Севера и Средней Азии. В то же время применение длинномерных секций позволяет сократить объемы работы в тяжелых трассовых условиях.
При сварке труб диаметром до 1020 мм на трубосварочных базах чаще всего применяют установки типаПАУ-600 с торцевыми вращателями и легкими переносными автоматами ПТ-56, работающими с проволокой диаметром 2 мм. Эти установки имеют источник питания на 600 А от дизельного привода. За последние годы для тяжелых труб диаметром 1020 мм и более созданы новые, более совершенствованные типы трубосварочных установок для сварки под флюсом, на которых механизированы операции не только сварки, но и сборки. Такая установка (типа ПАУ-1001; рис. 19.1) в отличие от установки ПАУ-600 имеет роликовый вращатель, исключающий неравномерное вращение тяжелых секций. Сварку ведут в двух ков, внутренняя подварка швов, панорамное просвечивание самоходными установками для контроля швов, ультразвуковой контроль швов и т. п. 6 связи с изложенным в 1974 г. были приняты специальные меры по повышению технического уровня строительства магистральных нефтепроводов и газопроводов, обеспечению большей надежности их эксплуатации.
Было предусмотрено улучшение свойств труб, создание новой и усовершенствование существующей технологии сварки трубопроводов различными способами, создание новых сварочных материалов и новых средств контроля швов.
В настоящее время при строительстве трубопроводов применяют различные способы сварки, при этом с учетом сварки труб на трубных заводах на автоматическую сварку под флюсом приходится около 90% общего объема сварки. Ручную сварку применяют практически только в полевых условиях для соединения труб между собой.
Для ускорения строительства и повышения надежности трубопроводов максимально сокращают объем сварки в полевых условиях за счет увеличения длины труб, поставляемых с трубосварочных заводов. Если 10-12 лет назад трубы имели длину б м, то в настоящее время трубы больших диаметров поставляют длиной в основном 12 м. Ведутся работы по изготовлению труб еще большей длины. Так, например, один из участков газопровода Средняя Азия- Центр построен в опытном порядке из труб диаметром 1020 мм, длиной 24 м, изготовленных Новомосковским трубным заводом. Расчеты показывают, что увеличение длины труб позволит существенно уменьшить число квалифицированных рабочих на строительстве трубопроводов и уменьшить стоимость оборудования для сборки и сварки.
Для повышения уровня механизации сварки в полевых условиях, увеличения производительности труда и улучшения качества кольцевых швов за последние годы Киевским филиалом СКВ «Газкопроизводительные установки для двухсторонней автоматической сварки под флюсом с предварительным изменением геометрии кромок .
Широкое внедрение в производство двухсторонней автоматической сварки под флюсом значительно повышает уровень комплексной механизации. Для решения этой задачи применительно к поворотным стыкам, в частности, потребовалось определить оптимальную форму и размеры подготовки торцов труб с увеличенным притуплением и создать специальные станки для их обработки’ непосредственно на трассах. Станки серийно выпускает Гомельский завод Минстанкопрома.
Следующее направление в механизации сварки секции-применение стыковой сварки непрерывным оплавлением. Стыковая сварка непрерывным оплавлением уже освоена для труб диаметром до 530 мм на полустационарных установках типа ТКУС, изготовляющих трубные секции. Для обеспечения требуемого качества стыков применили регулятор, который вычисляет и поддерживает оптимальные параметры режима в процессе сварки труб.
По инициативе ВНИИСТ, ИЭС им. Е. О. Патона и КФ СКВ «Газстроймашина» на Электростальском заводе тяжелого машиностроения разработана и испытывается мощная установка для стыковой сварки непрерывным оплавлением трехтрубных секций из труб 720- 1020 мм.
Основным способом сварки неповоротных стыков при соединении секции в нитку трубопровода в настоящее время все еще остается ручная сварка с использованием мощных гидравлических центраторов для сборки конструкции СКВ «Газстроймашина» (рис. 19.2). Производительность при ручной сварке потолочных стыков трубопроводов при применении внутренних центраторов зависит от организации сборочно-сварочных работ.
При сварке магистральных трубопроводов чаще всего применяют поточно расчлененный метод сварки отдельных секций, при котором трубопровод становится как-бы неподвижным конвейером, по которому с заданной скоростью пере-двигаются сборщики и сварщики, каждый из которых производит одну и ту же операцию. Например, сварщики в голове бригады на каждом следующем собранном стыке сваривают определенную часть корневого шва, а сварщики, двигающиеся вслед за головным звеном, сваривают определенные участки заполняющих слоев шва.
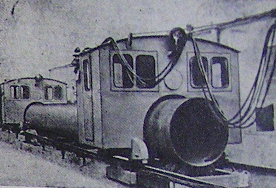
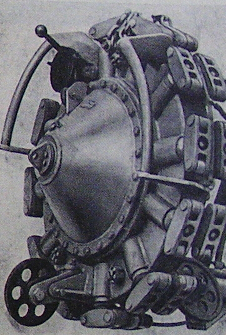
Производительность ручной сварки трубопроводов больших диаметров может быть увеличена за счет уменьшения количества присадочного металла. Для этого изменили характер подготовки кромок труб со стенкой толщиной 16 мм и более, при этом традиционную V-об-разную разделку с углом раскрытия кромок 70° заменили на фигурную (типа рюмки). Такая разделка на трубах диаметром 1420 мм уменьшила расход присадочного металла примерно на 20%. Для дальнейшего улучшения качества и повышения производительности неповоротной сварки, особенно труб большого диаметра, необходимо использовать систему автоматов, работающих в среде защитных газов поточно-расчлененным методом, подобно ручной сварке.
Одним из перспективных направлений работ по механизации сварки секций труб на трассе непосредственно в нитку трубопровода является развитие стыковой сварки непрерывным оплавлением передвижными агрегатами. Этот способ разработан ИЭС им. Е. О. Патона с участием ВНИИСТ и КФ СКВ «Газстрой- машина». Новый способ применен на строительстве трубопроводов после раз-работки специального оборудования, позволяющего оплавлять трубы при сравнительно низкой удельной мощности-до 2 кВт/см2 (благодаря применению специальных контурных трансформаторов).
Для стыковой сварки труб в полевых условиях были разработаны передвижные трубосварочные агрегаты типа КТСА и ТКУП (рис. 19.3), сваривающие трубы диаметром до 530 мм. В ИЭС им. Е. О. Патона был создан опытный агрегат для сварки труб диаметром 720 мм, перемещающийся внутри трубопровода.
В настоящее время ИЭС им. Е. О. Патона при участии Миннефтегазстроя, ряда министерств и научно-исследовательских организаций создал, испытал и внедрил внутритрубную самоходную электроконтактную установку «Север» для сварки труб диаметром 1220- 1420 мм в северных районах страны. Первую установку испытали на газопроводе Оренбург - государственная граница диаметром 1420 мм. В 1977-1979 гг. такие установки начали работать на северных трубопроводах.
Широкое внедрение автоматов для дуговой сварки неповоротных стыков трубопроводов, а также установок для стыковой сварки потребует нескольких лет и значительных затрат. Поэтому производительность неповоротной сварки трубопроводов в ближайшее время будет возрастать также за счет организации крупных бригад сварщиков-потолочников.
Качество и производительность сварочно-монтажных работ в значительной мере зависит от применяемых сварочных материалов . ВНИИСТ разработал и рекомендовал фтористокальциевые электроды типа ВСФ; фтористо-кальциевые электроды для сварки сверху вниз на спуск типа ВСФС и целлюлозные электроды типа ВСЦ также для сварки на спуск. Для автоматической сварки неповоротных стыков в среде углекислого газа применяют проволоку типа 08Г2С малого диаметра (0,8-1,2 мм). Сварку под флюсом ведут марганцовистыми или хромомолибденовыми проволоками под плавленными флюсами АН-348А, АН-22 или АН-47.
Применение труб большого диаметра из новых марок сталей с ограниченной свариваемостью потребовало разработать следующие новые технологические решения в области сварки.
Для обеспечения достаточной надежности сварки труб из высокопрочных сталей в ряде случаев оказалось необходимым подогревать стыки. Необходимость подогрева (и его температура) зависит от эквивалента углерода, толщины стенки трубы, температуры окружающего воздуха и типа электродов. Для сварки корня шва во ВНИИСТ были проведены теоретические и экспериментальные исследования этого вопроса и составлены специальные таблицы подогрева . Подогрев производят кольцевыми газовыми горелками, работающими на пропане.
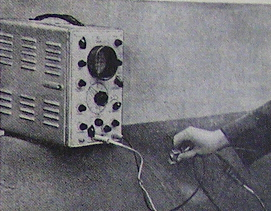
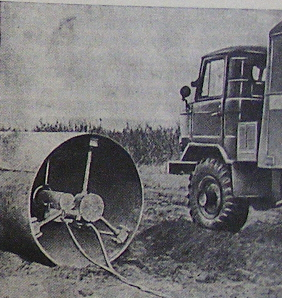
Второе важное технологическое мероприятие - применение внутренней подварки стыков на трубах диаметром 1020-1420 мм, что позволило предотвратить почти половину разрушений по
сварным швам. Подварка потребовала некоторого изменения организации сварочно-монтажных работ и дополнительных мероприятий по обеспечению техники безопасности. В СКВ Газстрой- машина разработано специальное оборудование для сварки изнутри трубы.
С целью обеспечения высокого качества сварных соединений и облегчения труда в полевых условиях на строительстве магистральных трубопроводов широко применяют малую механизацию. На рис. 19.4 показана зачистка сварных швов от шлака высокооборотными шлифовальными машинками (8000 об./мин) с безопасными абразивными кругами.
- Качество сварочно-монтажных работ на трубопроводах должно быть обеспечено за счет надежных методов контроля.
- Способы контроля сварных стыков магистральных трубопроводов и объем контроля определяются строительными нормами и правилами (СНиП).
- Основные требования к качеству сварки и контролю магистральных трубопроводов отражены в СНиП Ш.Д 42-80, в соответствии с которым способ контроля сварных стыков и его объем зависит от категории магистрального трубопровода.
- Наиболее ответственные участки трубопроводов относятся к I и II категориям (всего имеется четыре категории).
Практика строительства ответственных трубопроводов, в том числе диаметром 1420 мм, показала, что целесообразно увеличивать объем контроля на первом этапе строительства и сокращать его до требований СНиП только после того, как достигнуто высокое качество работы данной сварочно-монтажной организации.
Для контроля качества сварных швов магистральных трубопроводов в СССР применяют просвечивание рентгеновскими и гамма-лучами, магнитографический контроль и контроль ультразвуком. Для контроля трубопроводов рентгеновскими лучами широко применяют импульсные рентгеновские аппараты типа ИРА, которые используют для панорамного или направленного просвечивания труб любого диаметра (от 75 до 1420 мм включительно). Такие аппараты имеют малую массу небольшие габариты.
- В 1972 г. начато производство нового, более портативного импульсного рентгеновского аппарата РИНА-1Д, имеющего значительно большую частоту следования импульсов (15 Гц) и меньшую массу (масса блока составляет всего 5 кг).
- Этим аппаратом стык трубы 1420X17,0 мм просвечивают панорамно изнутри всего за 10 с. Можно направленно просвечивать через две стенки стыки трубы диаметром до 1020 мм включительно.
- Для контроля труб диаметром 720 мм и выше разработан рентгеновский аппарат РУП-160-6П с газовой изоляцией.
- Аппарат обеспечивает просвечивание при панорамном и направленном излучении.
Для просвечивания трубопроводов радиоактивными изотопами широко применяют гамма-дефектоскопы РИД-21 Г, «Газпром» и «Трасса», заряженные цезием-137. Первые два аппарата используют для направленного просвечивания, а «Трассу» также и для панорамного. В 1972 г. гамма-дефектоскопы «Газпром» и «Трасса» были модернизированы, что позволило заряжать их изотопом иридий-192 с большей разрешающей способностью благодаря чему эффективность этого метода не уступает рентгеновскому просвечиванию.
При просвечивании потолочных стыков трубопроводов больших диаметров весьма эффективно применять внутритрубную установку, снабженную мощным источником гамма-излучения, которая самостоятельно перемещается внутри сваренного трубопровода и автоматически панорамно просвечивает кольцевые стыки. Эта установка может работать и с рентгеновскими аппаратами типа ИРА-2Д и РИНА-1Д.
Для контроля стыков трубопроводов широко применяют разработанный во ВНИИСТ магнитографический способ контроля , при котором дефекты записывают на магнитную ленту с последующим воспроизведением с помощью, например, дефектоскопа МДУ-2У.
Этот дефектоскоп имеет два вида индикации: телевизионную (видео-индикация) и импульсную, обеспечивающую качественную и количественную оценку дефектов, записанных на магнитную ленту.
- Магнитографический метод контроля успешно применяют для сварных швов трубопроводов с толщиной стенки до 18 мм.
- Этот способ отличается полной безопасностью и высокой производительностью.
- Так, например, на объектах строительства трубопровода диаметром 1420 мм один контролер-магнитограф с помощником при нормальной организации труда может проконтролировать в течение рабочего дня до 15-18 поворотных сварных швов или до 12-14 потолочных швов.
В связи с увеличением толщины стенки современных сверхмощных трубопроводов необходимо применять ультразвуковую дефектоскопию (рис. 19.5). Чтобы существенно повысить производительность ультразвукового метода контроля, необходимо механизировать и автоматизировать все операции контроля.
Разрабатываются автоматизированные ультразвуковые установки для контроля кольцевых швов, сваренных электродуговой и электроконтактной сваркой.
Для контроля сварных соединений трубопроводов созданы специальные полустационарные и передвижные полевые испытательные лаборатории. Полу-стационарные лаборатории типа JIKG используют на трубосварочных базах, а передвижные лаборатории типа PMJI или BJIK (вездеходные) - для контроля неповоротных стыков трубопроводов (рис. 19.6).
Array ( => [~TAGS] => => 40509 [~ID] => 40509 => Технология сварки трубопровода [~NAME] => Технология сварки трубопровода => 1 [~IBLOCK_ID] => 1 => 115 [~IBLOCK_SECTION_ID] => 115 =>
Классификация трубопроводов
промысловые трубопроводы
магистральные трубопроводы
водоснабжение и канализация
Способы сварки трубопроводов
Таблица 1
Требования к трубам
В СНГ трубы применяются в соответствии с ГОСТ 8731 ... ГОСТ 8734 группы В, а также при соответствующем технико-экономическом обосновании - по ГОСТ 9567; трубы стальные электросварные - в соответствии с ГОСТ 20295 для труб с условным диаметром (Ду) до 800 мм включительно. Для труб Ду >
Требования к сборке труб
Предварительный подогрев
Таблица 2
(°С)ТП.П= 1440 Рcм - 392.
Таблица 3
[~DETAIL_TEXT] =>
Классификация трубопроводов
В зависимости от функционального назначения трубопровода подразделяют на:
промысловые трубопроводы
магистральные трубопроводы
трубопроводы пара и горячей воды
технологические трубопроводы
трубопроводы газоснабжения (распределительные)
водоснабжение и канализация
Значительный объем в сталях, применяемых для изготовления труб и строительства трубопроводов различного назначения, занимают низкоуглеродистые и низколегированные стали с пределом текучести до 500 МПа.
Поскольку технологические процессы сварки труб из указанных сталей при строительстве трубопроводов различного назначения практически мало чем отличаются друг от друга, а применяемые при этом руководящие нормативно-технические документы отражают различия только в требованиях к подготовке кромок, сборке, качеству сварных соединений и испытаниям на прочность и герметичность, то в дальнейшем мы рассмотрим общие положения технологического процесса изготовления на примере магистральных и распределительных (трубопроводов газоснабжения) трубопроводов.
Способы сварки трубопроводов
Способы сварки трубопроводов классифицируют как термические, термомеханические и механические. Термические способы включают все виды сварки плавлением (дуговая, газовая, плазменная, электронно-лучевая, лазерная и др. виды сварки. К термомеханическому классу относятся стыковая контактная сварка, сварка магнитоуправляемой дугой. К механическим способам относятся сварка трением и взрывом.
Различают методы сварки трубопроводов по типу носителей энергии (дуговая, газовая, плазменная, лазерная и др.); по условиям формирования соединения (свободное или принудительное формирование сварного шва); по способу защиты зоны сварки (под флюсом, в защитных газах, с использованием самозащитной электродной проволоки т.д.); по степени механизации и автоматизации процесса (ручная, механизированная, автоматизированная и роботизированная).
Для сварки магистральных трубопроводов наибольшее распространение получили дуговые методы сварки. Более 60% всех стыков на магистралях свариваются автоматической дуговой сваркой под флюсом. Дуговая сварка под флюсом используется только в тех случаях, когда существует возможность вращения стыка. Сварку трубопроводов под флюсом в основном автоматизированным способом применяют при изготовлении двух- и трехтрубных секций диаметром 219...1420 мм. Когда применение механизированных методов невозможно, используется ручная дуговая сварка.
Ручную дуговую сварку выполняют при различных пространственных положениях стыка - нижнем, вертикальном и потолочном. В процессе сварки вручную перемещают электрод по периметру стыка со скоростью 8.. .20 м/ч.
Сварка в защитном газе имеет разновидности: по типу защитного газа - сварка в инертных газах (аргон, гелий, их смесь), в активных газах (СО2, азот, водород), сварка в смеси инертного и активного газов (Аг + СО2; Аг + СО2 + О2); по типу электрода - плавящимся и неплавящимся (вольфрамовым) электродом; по степени механизации ручная, механизированная и автоматизированная сварка. Дуговую сварку в защитных газах применяют для сварки трубопроводом в различных пространственных положениях. Скорость ручной сварки 8...30 м/ч, механизированной и автоматизированной 20...60 м/ч. Для сварки трубопроводом применяют метод механизированной сварки порошковой проволокой с принудительным формированием шва, при котором функции защиты выполняют порошкообразные компоненты, заполняющие металлическую оболочку проволоки. По мере кристаллизации сварочной ванны наружное формирующее устройство и сварочная головка перемещаются по периметру стыка снизу вверх со скоростью 10...20 м/ч. Перспективна лазерная сварка трубопроводом, при которой носителем энергии служит лазерный луч. Скорость лазерной сварки - до 300 м/ч.
При стыковой контактной сварке непрерывным оплавлением процесс происходит автоматически по заданной программе. Продолжительность сварки одного стыка труб диаметром 1420 мм составляет 3...4 мин, цикл сварки одного стыка при строительстве трубопроводов -10... 15 мин.
Автоматическая сварка магнитоуправляемой дугой (или дугоконтактная сварка) отличается от стыковой контактной сварки способом нагрева кромок. При дугоконтактной сварке нагрев выполняется дугой, вращаемой магнитным полем по кромкам свариваемых труб с большой скоростью. Этот способ сварки применяют для сооружения трубопроводов малого (пока до 114 мм) диаметра.
Нормативные документы, применяемые при строительстве магистральных и распределительных трубопроводов
Главным нормативным документом, регламентирующим правила выполнения сборочно-сварочных работ при строительстве трубопроводов в СНГ являются «Строительные нормы и правила» на основе которых были разработаны «Сводные правила по производству сварочных работ и контролю качества сварных соединений» СП 105-34-96, а также СНиП 3.05.02.88 «Трубопроводы газоснабжения». В этих документах приводятся правила квалификационных испытаний сварщиков и контроля допускных стыков, правила подготовки труб к сварке, условия правки, ремонта и отбраковки труб, порядок сборки различных труб между собой и с трубопроводной арматурой, оговорены методы сварки и погодные условия при выполнении работ на трассе, нормативные документы регламентируют применение рекомендованных сварочных материалов, а также нормы и правила контроля сварных соединений трубопроводов, условия их выбраковки и ремонта.
В развитие основных положений указанных СНиПов разработаны технологические инструкции по сварке трубопроводов (ВСН 066-89 и ВБН А.3.1.-36-3-96 и методом контроля сварных стыков трубопроводов (ВСН 012-88). Эти инструкции регламентируют: основные положения технологии ручной и автоматической дуговой сварки кольцевых стыков труб, а также труб с запорной и распределительной арматурой магистральных и распределительных трубопроводов диаметром от 14 до 1420 мм с толщиной стенки от 1 до 26 мм, рассчитанных на давление не свыше 7,5 МПа; контроля сварных соединений и их ремонта; техники безопасности и производственной санитарии. По этим инструкциям разрешается сваривать трубы из сталей с нормативным временным сопротивлением разрыву до 590 МПа включительно. В инструкциях приведены технологические особенности сварки трубопроводов методами ручной дуговой сварки, автоматической сварки под флюсом, автоматической сварки в среде защитных газов и порошковой проволокой с принудительным формированием шва. Инструкции не распространяются на сварку трубопроводов специального назначения (для транспортировки аммиака, этилена, этанола, углекислоты и др.), а также трубопроводов для коррозионноактивных продуктов.
За рубежом при строительстве трубопроводов руководствуются национальными и международными стандартами (табл. 1), среди которых наибольшей популярностью пользуются АРI 1104, АРI 5D и ВS 4515. При контроле качества сварных соединений трубопровода, как правило, руководствуются международным стандартом ISО 8517 и европейским стандартом ЕN 25817.
Таблица 1
Требования к трубам
Для строительства магистральных и распределительных газопроводов применяются стальные бесшовные электросварные прямошовные и спиральношовные. Трубы диаметром до 1020 мм изготавливаются из спокойных и полуспокойных низколегированных сталей, трубы диаметром до 1420 мм - из низколегированных сталей в термически улучшенном или термомеханически упрочненном состоянии. Только для распределительных газопроводов низкого давления (до 0,005 МПа) допускается применение труб из кипящих низкоуглеродистых сталей.
В СНГ трубы применяются в соответствии с ГОСТ 8731 ... ГОСТ 8734 группы В, а также при соответствующем технико-экономическом обосновании - по ГОСТ 9567; трубы стальные электросварные - в соответствии с ГОСТ 20295 для труб с условным диаметром (Ду) до 800 мм включительно. Для труб Ду > 800 мм разрабатываются специальные технические условия, в которые должны включаться требования, изложенные ниже.
Готовые трубы маркируют, выбивая клеймами (холодной штамповкой) на расстоянии 250-500 мм от одного из концов трубы следующие данные: товарный знак или наименования предприятия - изготовителя; марку стали или ее условное обозначение; номер трубы; клеймо технического контроля; год изготовления. Участок клеймения четко обводят краской. Кроме того, на трубе несмываемой краской указывают ее диаметр и толщину стенки.
Импортные трубы изготавливаются и поставляются в основном по стандартам Американского нефтяного института (АРI), таких как: АРI-5 I (бесшовные и прямошовные трубы), АРI-513 (спиральношовные трубы для различных трубопроводов) АРI-51Х (трубы для трубопроводов высокого давления).
По этим стандартам трубные стали объединяются в группы по пределу текучести. Каждая группа сталей с одинаковыми значениями предела текучести в тысячах фунтов на 1 кв.дюйм. По этим стандартам существуют группы сталей: Х-42, Х-46, Х-52, Х-56, Х-60, Х-65, Х-70 с временным сопротивлением разрушению от 414 до 565 МПа. Стандарты АРI помимо механических свойств регламентируют процесс изготовления труб, химический состав стали, размеры, массу и длину трубы, давление при гидравлических испытаниях в процессе изготовления, методы неразрушающего контроля, которые применяют при изготовлении, условия ремонта труб и т.д. Обозначение трубы по стандарту АРI состоит из названия фирмыизготовителя труб, монограммы АРI (товарного знака, означающего, что данная труба изготовлена в соответствии с требованиями АРI), размера трубы в дюйма, массы одного фута трубы в фунтах, обозначения класса прочности стали и вида изготовления (S -бесшовные, Е - сварные прямошовные трубы, SW - спиральношовные трубы, Р - трубы с продольным швом, сваренные прессовыми методами), обозначения типа стали (Е - сталь, выплавленная в электропечах, М - высокопрочная низколегированная сталь), обозначения вида термообработки (NМ -нормализация или нормализация и отпуск, NО - закалка и отпуск, NS -высокий отпуск). Маркировка выполняется несмываемой краской. Трубы для магистральных трубопроводов изготавливаются из сталей с соотношением предела текучести к временному сопротивлению разрыву не более: 0,75 - для низкоуглеродистых сталей; 0,8 - для низколегированных нормализованных сталей; 0,85 - для дисперсионно-твердеющих нормализованных и термически улучшенных сталей; 0,9 - для сталей контролируемой прокатки.
Подготовка кромок труб под сварку
Перед началом сварочно-монтажных работ необходимо убедиться в том, что используемые трубы и детали трубопроводов имеют сертификаты качества и соответствуют проекту, техническим условиям на их поставку. Трубы и детали должны пройти входной контроль в соответствии с требованиями соответствующих стандартов и технических условий на трубы.
Концы труб и соединительных деталей должны иметь форму и размеры скоса кромок, соответствующие применяемым процессам сварки. При их несоответствии допускается механическая обработка кромок в трассовых условиях. Для труб небольшого диаметра (до 520 мм) возможно применение торцевателей, фаскоснимателей, труборезов и шлифмашинок. Для больших диаметров применяются орбитальные фрезерные машины, гидроабразивная резка и шлифмашинки. В отдельных случаях, при врезке катушек или выполнении захлестов, допускается применение термических способов подготовки кромок, таких как:
а) газокислородная резка с последующей механической зачисткой кромок абразивным кругом на глубину 0,1.. .0,2 мм;
б) воздушно-плазменная резка с последующей механической обработкой на глубину до 1 мм - вследствие насыщения кромки азотом (при использовании аргона в качестве плазмообразующего газа механическая обработка не требуется); в) воздушно-дуговая резка с последующей зашлифовкой на глубину до 0,5 мм (науглераживание кромок);
г) строжка и резка специальными электродами типа АНР-2М, АНР-3 или ОК.21.03, после которых не требуется механическая обработка.
Перед сборкой труб необходимо очистить внутреннюю полость труб от попавших туда грунта, грязи, снега, а также зачистить до металлического блеска кромки и прилегающие к ним внутреннюю и наружную поверхность труб и соединительных деталей на ширину не менее 10 мм.
Участки усиления наружных заводских швов, прилегающие к свариваемому торцу трубы, рекомендуется ошлифовывать до высоты О..Д5 мм на расстоянии от торца не менее 10 мм.
Все трубы поступают на трассу с заводов с разделкой кромок, предназначенной для ручной дуговой сварки покрытыми электродами. Эта разделка (рис. 1, а) имеет для труб любого диаметра при толщине стенки более 4 мм угол скоса кромок 25-30° и притупление 1-2,6 мм. При толщине стенки 16 мм и более трубы большого диаметра могут поставляться с комбинированной разделкой кромок в соответствии с рис. 1, б.
Размер В зависит от толщины стенки и составляет:
7 мм - при толщине стенки трубы 15... 19 мм
8 мм - при толщине стенки трубы 19...21,5 мм
10 мм - при толщине стенки трубы 21,5... 26 мм.
Рис. 1. Типы разделки кромок труб для ручной дуговой сварки (а, б), автоматической сварки в среде защитных газов (в), автоматической сварки под флюсом (г, д, е, ж) и порошковой проволокой с принудительным формированием (а, б).
Для трубопроводов Ду 1000 мм и свыше, когда предусмотрено выполнение подварочного корневого шва изнутри, рекомендуется разделка представленная на рис.1, в. При строительстве распределительных трубопроводов допускается ручная дуговая сварка труб без разделки кромок с толщиной стенки до 4 мм. Кроме того, для трубопроводов диаметром до 152 мм возможно применение газовой сварки (без разделки кромок - до 3 мм, и односторонним скосом кромок - до 5 мм).
Соединение разностенных труб на трассе допускается без дополнительной обработки кромок:
для толщин стенок не более 12,5 мм, если разность толщины не превышает 2 мм;
для толщин стенок свыше 12,5 мм, если разность толщины не превышает 3 мм. В этом случае смещение стыкуемых кромок не допускается.
Соединение труб или труб с запорной и распределительной арматурой с большей разностью толщин стенок осуществляют посредством вварки между стыкуемыми элементами переходников заводского изготовления или вставок из труб промежуточной толщины длиной не менее 250 мм.
Допускается выполнять непосредственную сборку и сварку труб или труб с деталями трубопроводов при разностенности до 1,5 толщин при специальной обработке, прилегающей к торцу поверхности более толстой трубы или детали (рис.2, а). Сварка захлесточных стыков разностенных труб не допускается.
Непосредственное соединение труб с запорной и распределительной арматурой разрешается при условии, если толщина стыкуемого торца арматуры не превышает 1,5 толщины стенки трубы с подготовкой патрубка арматуры согласно (рис. 2, б). Указанная подготовка должна быть осуществлена заводом-поставщиком.
Рис. 2. Подготовка для сварки торцов труб и деталей с разной толщиной стенки.
Требования к сборке труб
Сборка стыков труб должна гарантировать:
Перпендикулярность стыка к оси трубопровода. Отклонение от перпендикулярности не должно превышать 2 мм;
равномерность по периметру зазора, находящегося в пределах значений, регламентированных соответствующими стандартами и инструкциями;
минимально возможную величину смещения кромок, регистрируемую универсальными шаблонами, не превышающую допустимых значений (для магистральных трубопроводов - 0,2 толщины стенки, но не более 3 мм, для распределительных - (0,15 толщины стенки + 0,5 мм);
смешение продольных заводских швов относительно друг друга на расстояние не менее 100 мм - для труб диаметром более 100 мм и на 1/3 длины окружности - для труб диаметром менее 100 мм. В случае технической невозможности выполнения указанных требований назначается дополнительный ультразвуковой контроль сварочного соединения на данном участке стыка.
При изготовлении труб большого диаметра, корпусов цилиндров из обечаек применяют следующие виды сборки и сварки - "Сборка и сварка обечаек корпуса."
Предварительный подогрев
Предварительный подогрев является одной из важнейших технологических операций, позволяющих регулировать термический цикл сварки. Известно, что структура и свойства сварного соединения в значительной степени определяются скоростью охлаждения металла в интервале температур 800-500°С (наименьшей устойчивости аустенита). При высоких скоростях охлаждения возможно образование закалочных структур типа мартенсит в ЗТВ, обладающих высокой прочностью и низкой пластичностью, а также склонностью к образованию холодных трещин. Особенно это относится к низколегированным сталям с эквивалентом углерода 0,43% и выше. Эти стали весьма чувствительны к действию термического цикла, к концентраторам, а зона термического влияния склонна к охрупчиванию. Наиболее ярко эти явления проявляются при ручной дуговой сварке, когда скорость охлаждения металла ЗТВ может достигать 70°С/с. При заданной толщине стенки трубы регулировать скорость охлаждения зоны термического влияния можно изменяя начальную температуру стыкующих кромок предварительным подогревом. Особенно важно это при сварке корня шва электродами с целлюлозным покрытием, когда скорость охлаждения максимальна по сравнению со сваркой других слоев шва, уменьшена погонная энергия сварки (скорость сварки такими электродами вдвое превышает скорость сварки электродами с основным покрытием) и увеличена склонность и образованию холодных трещин за счет повышения содержания диффузионного водорода в металле шва. Предварительный подогрев не только уменьшает вероятность образования закалочных структур в ЗТВ, но и создает условия для активной эвакуации диффузионного водорода из металла шва и указанной зоны. Что, в свою очередь, повышает стойкость сварных соединений против образования холодных трещин, особенно при использовании электродов с целлюлозным покрытием, когда содержание водорода в шве может достигать 50 мм на 100 г наплавленного металла.
Температуру предварительного подогрева выбирают в зависимости от химсостава стали (по эквиваленту углерода), толщины станки трубы, температуры окружающего воздуха и вида электродного покрытия. Эти параметры, как правило, регламентируются соответствующими стандартами и технологическими инструкциями. Так, например, в СНГ руководствуются ВСН 066-89 (табл. 2). При сварке электродами с целлюлозным покрытием температура предварительного подогрева повышается на 75 °С.
Таблица 2
За рубежом часто при выборе подогрева оперируют показателем трещиностойкости сварных соединений, определяемый по формуле Ито-Беесио:
где: [Н] - содержание диффузионного водорода, мм/100 г;
t - толщина свариваемых пластин, мм. Температура подогрева определяется на эмпирической формуле:
(°С)ТП.П= 1440 Рcм - 392.
Предварительный и, при необходимости, сопутствующий подогрев следует осуществлять нагревательными устройствами (газовыми или электрическими), обеспечивающими равномерный нагрев металла по всему периметру свариваемого стыка. Ширина зоны разо¬грева труб в каждую сторону от шва должна быть не менее 75 мм.
Температуру предварительного и сопутствующего подогрева при соединении труб (или трубы с деталью) из различных марок стали или с различной толщиной стенки, которые должны быть нагреты на разные температуры, устанавливают по максимальному значению.
Технология и техника ручной дуговой сварки
Почти 60% объема сварочных работ при строительстве трубопроводов приходится на ручную дуговую сварку. Это соединение секций или отдельных труб в непрерывную нитку, сварка переходов через естественные и искусственные преграды, сварка захлестов, вварка катушек, крановых узлов, отводов и др.
Технология ручной дуговой сварки определяется прежде всего материалом труб, подлежащих сварке. В зависимости от марки стали трубы и условий эксплуатации выбирают сварочные материалы. После этого устанавливают технологию и технику сварки, а также схему организации работ, при этом руководствуются заданным темпом строительства трубопровода. При заданных сварочных материалах технология сварки зависит от диаметра и толщины стенки трубы.
Беспрекословным правилом при строительстве магистральных и распределительных трубопроводов есть требование к минимальному количеству слоев в шве. Для труб с толщиной стенки 6 мм и менее - 2 слоя, с толщиной стенки более 6 мм - 3 слоя.
Наиболее ответственным является корневой слой шва. Он должен надежно проплавлять кромки свариваемых труб и образовывать на внутренней поверхности шва равномерный обратный валик с усилением 1-3 мм. Допускается на отдельных участках стыка длиной не более 50 мм (на каждые 350 мм шва) ослабление корня шва (мениск) величиной до 10-15% от толщины стенки трубы. Наружная поверхность корневого слоя должна быть гладкой, мелкочешуйчатой и иметь плавное сопряжение с боковыми поверхностями разделки. Оптимальной формой наружной поверхности шва можно выполнять как шлифовальной машинкой, так и пневмомолотком в соответствии с требованиями инструкции.
При сварке труб диаметром 1020 мм и более после сварки корня шва рекомендуется выполнить подварку корневого слоя изнутри трубы в тех местах, где имеется не провар корня, и обязательно в нижней четверти периметра стыка (изнутри), т.е. на том участке, который при сварке корня шва снаружи выполнялся в потолочном положении. При ручной сварке корня шва поворотных стыков труб большого диаметра подварку выполняют по всему периметру стыка. Подеарочный шов обеспечивает провар корня, он должен иметь мелкочешуйчатую поверхность, плавно сопрягающуюся с внутренней поверхностью трубы без подрезов и других дефектов. Усиление подварочного шва должно составлять не менее 1 и не более 3 мм. Подварку выполняют электродами основного типа диаметром 3-4 мм.
Заполняющие слои шва надежно сплавляются между собой и проплавляют кромки свариваемых труб. После каждого слоя шва необходимо обязательно очищать поверхности шва от шлака.
Облицовочный шов имеет плавное очертание и сопряжение с поверхностью трубы, без подрезов и других видимых дефектов. Усиление шва должно быть не менее 1 и не более 3 мм. Ширина шва перекрывает ширину разделки на 2-3 мм в каждую сторону.
В конце смены сварной стык должен быть заварен полностью. Это требование вызвано тем, что трубопровод в течение суток претерпевает действие изменения температуры окружающего воздуха, которое особенно существенно при смене для ночью и ночи - днем. Изменение температуры вызывает возникновение в трубах и сварных стыках напряжений, которые могут быть весьма высокими.
Если стык заварен не полностью, то в ослабленном сечении шва напряжения могут превысить предел текучести и даже временное сопротивление разрушению металла шва и стык разрушится. Особенно опасна эта ситуация при отрицательных температурах воздуха, когда снижается пластичность металла.
В зависимости от типа рекомендуемых электродов существует 3 наиболее распространенных схемы сварки: сварка стыка электродами с основным покрытием, сварка стыка электродами газозащитного типа, сварка корня шва и горячего прохода электродами газозащитного типа, а заполняющих и облицовочного слоев - электродами с основным покрытием.
Сварку электродами с основным покрытием выполняют снизу вверх с поперечными колебаниями, амплитуда которых зависит от ширины разделки стыка. При поточно-расчлененном методе сварки каждый сварщик выполняет определенный участок шва, положение которого зависит от числа сварщиков, работающих одновременно на одном стыке. На трубах большого диаметра их число может достигать четырех. Как правило, если сварщиков двое, то они выполняют сварку снизу, от надира, и идут вверх по периметру в направлении (по циферблату часов) 6-3-12 и 6-9-12. При этом в потолочной части стыка замок следует смещать на 50-60 мм от нижней точки окружности трубы. В двух смежных слоях замки должны отстоять друг от друга не менее чем на 50-100 мм. Если сварщиков четверо, то первая пара варит участок стыка (по циферблату) 6-3 и 6-9, а вторая пара - 3-12 и 9-12.
Схема последовательности наложения двух слоев при сварке снизу вверх электродами с основным покрытием приведена на рис. 3, а. Все последующие нечетные слои выполняют по схеме первого слоя, все четные - по схеме второго слоя. Римские цифры показывают последовательность сварки отдельных участков шва. В зависимости от пространственного положения сварки рекомендуются значения тока, приведенные в табл.3.
При использовании электродов с покрытием основного вида следует применять только аттестованные для трубопроводного строительства марки электродов.
Таблица 3
При использовании электродов газозащитного типа сварку корня шва выполняют сверху вниз без колебательных движений, опираясь концом электрода на кромки свариваемых труб. Сварку выполняют постоянным током обратной или прямой полярности при напряжении холостого хода источника питания не менее 75В. Значения сварочного тока при сварке электродами диаметром 3,25 мм не должны превышать 100-110А; при сварке электродами диаметром 4 мм в нижнем и полувертикальном положении 120-160А, в остальных положениях 100-140А. Скорость сварки следует поддерживать в диапазоне 16-22 м/ч. Изменяя в процессе сварки угол наклона электрода от 40 до 90°, сварщик сохраняет образующееся при сквозном проплавлении кромок технологическое окно, через которое он наблюдает за оплавлением кромок.
Для снижения уровня остаточных сварочных напряжений в сварном соединении периметр неповоротного стыка разбивается на симметричные, диаметрально противоположные участки и многослойная сварка выполняется в последовательности, приведенной на рис. 4. Больший эффект снижения сварочных напряжений и деформации дает применение обратноступенчатого метода сварки и одновременное заполнение разделки двумя или четырьмя сварщиками.
При сварке трубопроводов небольшого диаметра (до 530 мм) с целью уменьшения объема монтажных работ в траншее часто практикуется укрупнение в секции труб сваркой с поворотом стыков на 90 или 180°. Трубу делят по окружности на четыре примерно одинаковых по длине участка. Заварив участки 1 и 2 стык поворачивают на 90° для сварки участков 3 и 4 (рис. 5). Затем, выполняя очередной поворот на 90°, производят последовательносварку участков 5 и 6, 7 и 8.
В другом случае, после сварки участков 1 и 2 (рис. 6) выполняют поворот стыкуемых труб на 180° для сварки участков 3 и 4. Затем поворот на 90° и 180° для сварки участков 5 и 6, 7 и 8 соответственно.
Рис.5 . Сварка с поворотом труб на 90°: а - первого слоя, б - второго, 1...8 - последовательность выполнения участков слоя.
Рис.6 . Сварка с поворотом труб на 180°: а - первого слоя, б - второго, 1...8 - последовательность выполнения участков слоя.
=> html [~DETAIL_TEXT_TYPE] => html => Классификация трубопроводов
В зависимости от функционального назначения трубопровода подразделяют на: [~PREVIEW_TEXT] => Классификация трубопроводов В зависимости от функционального назначения трубопровода подразделяют на: => text [~PREVIEW_TEXT_TYPE] => text => [~DETAIL_PICTURE] => => 15.12.2016 15:16:53 [~TIMESTAMP_X] => 15.12.2016 15:16:53 => 15.12.2016 [~ACTIVE_FROM] => 15.12.2016 => /news/ [~LIST_PAGE_URL] => /news/ => /news/115/40509/ [~DETAIL_PAGE_URL] => /news/115/40509/ => / [~LANG_DIR] => / => tekhnologiya_svarki_truboprovoda [~CODE] => tekhnologiya_svarki_truboprovoda => 40509 [~EXTERNAL_ID] => 40509 => news [~IBLOCK_TYPE_ID] => news => news [~IBLOCK_CODE] => news => clothes_news_s1 [~IBLOCK_EXTERNAL_ID] => clothes_news_s1 => s1 [~LID] => s1 => => 15.12.2016 => Array ( => Технология сварки трубопровода => технология сварки трубопровода => Классификация трубопроводов В зависимости от функционального назначения трубопровода подразделяют на: => Технология сварки трубопровода => Технология сварки трубопровода => технология сварки трубопровода => Классификация трубопроводов В зависимости от функционального назначения трубопровода подразделяют на: => Технология сварки трубопровода => Технология сварки трубопровода => Технология сварки трубопровода => Технология сварки трубопровода => Технология сварки трубопровода => Технология сварки трубопровода => Технология сварки трубопровода => Технология сварки трубопровода => Технология сварки трубопровода) => Array ( =>) => Array () => Array ( => 1 [~ID] => 1 => 15.02.2016 17:09:48 [~TIMESTAMP_X] => 15.02.2016 17:09:48 => news [~IBLOCK_TYPE_ID] => news => s1 [~LID] => s1 => news [~CODE] => news => Пресс-центр [~NAME] => Пресс-центр => Y [~ACTIVE] => Y => 500 [~SORT] => 500 => /news/ [~LIST_PAGE_URL] => /news/ => #SITE_DIR#/news/#SECTION_ID#/#ELEMENT_ID#/ [~DETAIL_PAGE_URL] => #SITE_DIR#/news/#SECTION_ID#/#ELEMENT_ID#/ => #SITE_DIR#/news/#SECTION_ID#/ [~SECTION_PAGE_URL] => #SITE_DIR#/news/#SECTION_ID#/ => [~PICTURE] => => [~DESCRIPTION] => => text [~DESCRIPTION_TYPE] => text => 24 [~RSS_TTL] => 24 => Y [~RSS_ACTIVE] => Y => N [~RSS_FILE_ACTIVE] => N => 0 [~RSS_FILE_LIMIT] => 0 => 0 [~RSS_FILE_DAYS] => 0 => N [~RSS_YANDEX_ACTIVE] => N => clothes_news_s1 [~XML_ID] => clothes_news_s1 => [~TMP_ID] => => Y [~INDEX_ELEMENT] => Y => Y [~INDEX_SECTION] => Y => N [~WORKFLOW] => N => N [~BIZPROC] => N => L [~SECTION_CHOOSER] => L => [~LIST_MODE] => => S [~RIGHTS_MODE] => S => N [~SECTION_PROPERTY] => N => N [~PROPERTY_INDEX] => N => 1 [~VERSION] => 1 => 0 [~LAST_CONV_ELEMENT] => 0 => [~SOCNET_GROUP_ID] => => [~EDIT_FILE_BEFORE] => => [~EDIT_FILE_AFTER] => => Разделы [~SECTIONS_NAME] => Разделы => Раздел [~SECTION_NAME] => Раздел => Новости [~ELEMENTS_NAME] => Новости => Новость [~ELEMENT_NAME] => Новость => [~CANONICAL_PAGE_URL] => => clothes_news_s1 [~EXTERNAL_ID] => clothes_news_s1 => / [~LANG_DIR] => / => www.alfa-industry.ru [~SERVER_NAME] => www.alfa-industry.ru) => Array ( => Array ( => Array ( => 115 [~ID] => 115 => 2015-11-25 18:37:33 [~TIMESTAMP_X] => 2015-11-25 18:37:33 => 2 [~MODIFIED_BY] => 2 => 2015-09-29 20:10:16 [~DATE_CREATE] => 2015-09-29 20:10:16 => 1 [~CREATED_BY] => 1 => 1 [~IBLOCK_ID] => 1 => [~IBLOCK_SECTION_ID] => => Y [~ACTIVE] => Y => Y [~GLOBAL_ACTIVE] => Y => 500 [~SORT] => 500 => Технические статьи [~NAME] => Технические статьи => [~PICTURE] => => 27 [~LEFT_MARGIN] => 27 => 28 [~RIGHT_MARGIN] => 28 => 1 [~DEPTH_LEVEL] => 1 => [~DESCRIPTION] => => text [~DESCRIPTION_TYPE] => text => ТЕХНИЧЕСКИЕ СТАТЬИ [~SEARCHABLE_CONTENT] => ТЕХНИЧЕСКИЕ СТАТЬИ => [~CODE] => => 115 [~XML_ID] => 115 => [~TMP_ID] => => [~DETAIL_PICTURE] => => [~SOCNET_GROUP_ID] => => /news/ [~LIST_PAGE_URL] => /news/ => /news/115/ [~SECTION_PAGE_URL] => /news/115/ => news [~IBLOCK_TYPE_ID] => news => news [~IBLOCK_CODE] => news => clothes_news_s1 [~IBLOCK_EXTERNAL_ID] => clothes_news_s1 => 115 [~EXTERNAL_ID] => 115 => Array ( => Технические статьи => технические статьи => => Технические статьи => Технические статьи => технические статьи => => Технические статьи => Технические статьи => Технические статьи => Технические статьи => Технические статьи => Технические статьи => Технические статьи => Технические статьи => Технические статьи)))) => /news/115/)
Технология сварки трубопровода
Классификация трубопроводов
В зависимости от функционального назначения трубопровода подразделяют на:
промысловые трубопроводы
магистральные трубопроводы
трубопроводы пара и горячей воды
технологические трубопроводы
трубопроводы газоснабжения (распределительные)
водоснабжение и канализация
Значительный объем в сталях, применяемых для изготовления труб и строительства трубопроводов различного назначения, занимают низкоуглеродистые и низколегированные стали с пределом текучести до 500 МПа.
Поскольку технологические процессы сварки труб из указанных сталей при строительстве трубопроводов различного назначения практически мало чем отличаются друг от друга, а применяемые при этом руководящие нормативно-технические документы отражают различия только в требованиях к подготовке кромок, сборке, качеству сварных соединений и испытаниям на прочность и герметичность, то в дальнейшем мы рассмотрим общие положения технологического процесса изготовления на примере магистральных и распределительных (трубопроводов газоснабжения) трубопроводов.
Способы сварки трубопроводов
Способы сварки трубопроводов классифицируют как термические, термомеханические и механические. Термические способы включают все виды сварки плавлением (дуговая, газовая, плазменная, электронно-лучевая, лазерная и др. виды сварки. К термомеханическому классу относятся стыковая контактная сварка, сварка магнитоуправляемой дугой. К механическим способам относятся сварка трением и взрывом.
Различают методы сварки трубопроводов по типу носителей энергии (дуговая, газовая, плазменная, лазерная и др.); по условиям формирования соединения (свободное или принудительное формирование сварного шва); по способу защиты зоны сварки (под флюсом, в защитных газах, с использованием самозащитной электродной проволоки т.д.); по степени механизации и автоматизации процесса (ручная, механизированная, автоматизированная и роботизированная).
Для сварки магистральных трубопроводов наибольшее распространение получили дуговые методы сварки. Более 60% всех стыков на магистралях свариваются автоматической дуговой сваркой под флюсом. Дуговая сварка под флюсом используется только в тех случаях, когда существует возможность вращения стыка. Сварку трубопроводов под флюсом в основном автоматизированным способом применяют при изготовлении двух- и трехтрубных секций диаметром 219...1420 мм. Когда применение механизированных методов невозможно, используется ручная дуговая сварка.
Ручную дуговую сварку выполняют при различных пространственных положениях стыка - нижнем, вертикальном и потолочном. В процессе сварки вручную перемещают электрод по периметру стыка со скоростью 8.. .20 м/ч.
Сварка в защитном газе имеет разновидности: по типу защитного газа - сварка в инертных газах (аргон, гелий, их смесь), в активных газах (СО2, азот, водород), сварка в смеси инертного и активного газов (Аг + СО2; Аг + СО2 + О2); по типу электрода - плавящимся и неплавящимся (вольфрамовым) электродом; по степени механизации ручная, механизированная и автоматизированная сварка. Дуговую сварку в защитных газах применяют для сварки трубопроводом в различных пространственных положениях. Скорость ручной сварки 8...30 м/ч, механизированной и автоматизированной 20...60 м/ч. Для сварки трубопроводом применяют метод механизированной сварки порошковой проволокой с принудительным формированием шва, при котором функции защиты выполняют порошкообразные компоненты, заполняющие металлическую оболочку проволоки. По мере кристаллизации сварочной ванны наружное формирующее устройство и сварочная головка перемещаются по периметру стыка снизу вверх со скоростью 10...20 м/ч. Перспективна лазерная сварка трубопроводом, при которой носителем энергии служит лазерный луч. Скорость лазерной сварки - до 300 м/ч.
При стыковой контактной сварке непрерывным оплавлением процесс происходит автоматически по заданной программе. Продолжительность сварки одного стыка труб диаметром 1420 мм составляет 3...4 мин, цикл сварки одного стыка при строительстве трубопроводов -10... 15 мин.
Автоматическая сварка магнитоуправляемой дугой (или дугоконтактная сварка) отличается от стыковой контактной сварки способом нагрева кромок. При дугоконтактной сварке нагрев выполняется дугой, вращаемой магнитным полем по кромкам свариваемых труб с большой скоростью. Этот способ сварки применяют для сооружения трубопроводов малого (пока до 114 мм) диаметра.
Нормативные документы, применяемые при строительстве магистральных и распределительных трубопроводов
Главным нормативным документом, регламентирующим правила выполнения сборочно-сварочных работ при строительстве трубопроводов в СНГ являются «Строительные нормы и правила» на основе которых были разработаны «Сводные правила по производству сварочных работ и контролю качества сварных соединений» СП 105-34-96, а также СНиП 3.05.02.88 «Трубопроводы газоснабжения». В этих документах приводятся правила квалификационных испытаний сварщиков и контроля допускных стыков, правила подготовки труб к сварке, условия правки, ремонта и отбраковки труб, порядок сборки различных труб между собой и с трубопроводной арматурой, оговорены методы сварки и погодные условия при выполнении работ на трассе, нормативные документы регламентируют применение рекомендованных сварочных материалов, а также нормы и правила контроля сварных соединений трубопроводов, условия их выбраковки и ремонта.
В развитие основных положений указанных СНиПов разработаны технологические инструкции по сварке трубопроводов (ВСН 066-89 и ВБН А.3.1.-36-3-96 и методом контроля сварных стыков трубопроводов (ВСН 012-88). Эти инструкции регламентируют: основные положения технологии ручной и автоматической дуговой сварки кольцевых стыков труб, а также труб с запорной и распределительной арматурой магистральных и распределительных трубопроводов диаметром от 14 до 1420 мм с толщиной стенки от 1 до 26 мм, рассчитанных на давление не свыше 7,5 МПа; контроля сварных соединений и их ремонта; техники безопасности и производственной санитарии. По этим инструкциям разрешается сваривать трубы из сталей с нормативным временным сопротивлением разрыву до 590 МПа включительно. В инструкциях приведены технологические особенности сварки трубопроводов методами ручной дуговой сварки, автоматической сварки под флюсом, автоматической сварки в среде защитных газов и порошковой проволокой с принудительным формированием шва. Инструкции не распространяются на сварку трубопроводов специального назначения (для транспортировки аммиака, этилена, этанола, углекислоты и др.), а также трубопроводов для коррозионноактивных продуктов.
За рубежом при строительстве трубопроводов руководствуются национальными и международными стандартами (табл. 1), среди которых наибольшей популярностью пользуются АРI 1104, АРI 5D и ВS 4515. При контроле качества сварных соединений трубопровода, как правило, руководствуются международным стандартом ISО 8517 и европейским стандартом ЕN 25817.
Таблица 1
Требования к трубам
Для строительства магистральных и распределительных газопроводов применяются стальные бесшовные электросварные прямошовные и спиральношовные. Трубы диаметром до 1020 мм изготавливаются из спокойных и полуспокойных низколегированных сталей, трубы диаметром до 1420 мм - из низколегированных сталей в термически улучшенном или термомеханически упрочненном состоянии. Только для распределительных газопроводов низкого давления (до 0,005 МПа) допускается применение труб из кипящих низкоуглеродистых сталей.
В СНГ трубы применяются в соответствии с ГОСТ 8731 ... ГОСТ 8734 группы В, а также при соответствующем технико-экономическом обосновании - по ГОСТ 9567; трубы стальные электросварные - в соответствии с ГОСТ 20295 для труб с условным диаметром (Ду) до 800 мм включительно. Для труб Ду > 800 мм разрабатываются специальные технические условия, в которые должны включаться требования, изложенные ниже.
Готовые трубы маркируют, выбивая клеймами (холодной штамповкой) на расстоянии 250-500 мм от одного из концов трубы следующие данные: товарный знак или наименования предприятия - изготовителя; марку стали или ее условное обозначение; номер трубы; клеймо технического контроля; год изготовления. Участок клеймения четко обводят краской. Кроме того, на трубе несмываемой краской указывают ее диаметр и толщину стенки.
Импортные трубы изготавливаются и поставляются в основном по стандартам Американского нефтяного института (АРI), таких как: АРI-5 I (бесшовные и прямошовные трубы), АРI-513 (спиральношовные трубы для различных трубопроводов) АРI-51Х (трубы для трубопроводов высокого давления).
По этим стандартам трубные стали объединяются в группы по пределу текучести. Каждая группа сталей с одинаковыми значениями предела текучести в тысячах фунтов на 1 кв.дюйм. По этим стандартам существуют группы сталей: Х-42, Х-46, Х-52, Х-56, Х-60, Х-65, Х-70 с временным сопротивлением разрушению от 414 до 565 МПа. Стандарты АРI помимо механических свойств регламентируют процесс изготовления труб, химический состав стали, размеры, массу и длину трубы, давление при гидравлических испытаниях в процессе изготовления, методы неразрушающего контроля, которые применяют при изготовлении, условия ремонта труб и т.д. Обозначение трубы по стандарту АРI состоит из названия фирмыизготовителя труб, монограммы АРI (товарного знака, означающего, что данная труба изготовлена в соответствии с требованиями АРI), размера трубы в дюйма, массы одного фута трубы в фунтах, обозначения класса прочности стали и вида изготовления (S -бесшовные, Е - сварные прямошовные трубы, SW - спиральношовные трубы, Р - трубы с продольным швом, сваренные прессовыми методами), обозначения типа стали (Е - сталь, выплавленная в электропечах, М - высокопрочная низколегированная сталь), обозначения вида термообработки (NМ -нормализация или нормализация и отпуск, NО - закалка и отпуск, NS -высокий отпуск). Маркировка выполняется несмываемой краской. Трубы для магистральных трубопроводов изготавливаются из сталей с соотношением предела текучести к временному сопротивлению разрыву не более: 0,75 - для низкоуглеродистых сталей; 0,8 - для низколегированных нормализованных сталей; 0,85 - для дисперсионно-твердеющих нормализованных и термически улучшенных сталей; 0,9 - для сталей контролируемой прокатки.
Подготовка кромок труб под сварку
Перед началом сварочно-монтажных работ необходимо убедиться в том, что используемые трубы и детали трубопроводов имеют сертификаты качества и соответствуют проекту, техническим условиям на их поставку. Трубы и детали должны пройти входной контроль в соответствии с требованиями соответствующих стандартов и технических условий на трубы.
Концы труб и соединительных деталей должны иметь форму и размеры скоса кромок, соответствующие применяемым процессам сварки. При их несоответствии допускается механическая обработка кромок в трассовых условиях. Для труб небольшого диаметра (до 520 мм) возможно применение торцевателей, фаскоснимателей, труборезов и шлифмашинок. Для больших диаметров применяются орбитальные фрезерные машины, гидроабразивная резка и шлифмашинки. В отдельных случаях, при врезке катушек или выполнении захлестов, допускается применение термических способов подготовки кромок, таких как:
а) газокислородная резка с последующей механической зачисткой кромок абразивным кругом на глубину 0,1.. .0,2 мм;
б) воздушно-плазменная резка с последующей механической обработкой на глубину до 1 мм - вследствие насыщения кромки азотом (при использовании аргона в качестве плазмообразующего газа механическая обработка не требуется); в) воздушно-дуговая резка с последующей зашлифовкой на глубину до 0,5 мм (науглераживание кромок);
г) строжка и резка специальными электродами типа АНР-2М, АНР-3 или ОК.21.03, после которых не требуется механическая обработка.
Перед сборкой труб необходимо очистить внутреннюю полость труб от попавших туда грунта, грязи, снега, а также зачистить до металлического блеска кромки и прилегающие к ним внутреннюю и наружную поверхность труб и соединительных деталей на ширину не менее 10 мм.
Участки усиления наружных заводских швов, прилегающие к свариваемому торцу трубы, рекомендуется ошлифовывать до высоты О..Д5 мм на расстоянии от торца не менее 10 мм.
Все трубы поступают на трассу с заводов с разделкой кромок, предназначенной для ручной дуговой сварки покрытыми электродами. Эта разделка (рис. 1, а) имеет для труб любого диаметра при толщине стенки более 4 мм угол скоса кромок 25-30° и притупление 1-2,6 мм. При толщине стенки 16 мм и более трубы большого диаметра могут поставляться с комбинированной разделкой кромок в соответствии с рис. 1, б.
Размер В зависит от толщины стенки и составляет:
7 мм - при толщине стенки трубы 15... 19 мм
8 мм - при толщине стенки трубы 19...21,5 мм
10 мм - при толщине стенки трубы 21,5... 26 мм.
Рис. 1. Типы разделки кромок труб для ручной дуговой сварки (а, б), автоматической сварки в среде защитных газов (в), автоматической сварки под флюсом (г, д, е, ж) и порошковой проволокой с принудительным формированием (а, б).
Для трубопроводов Ду 1000 мм и свыше, когда предусмотрено выполнение подварочного корневого шва изнутри, рекомендуется разделка представленная на рис.1, в. При строительстве распределительных трубопроводов допускается ручная дуговая сварка труб без разделки кромок с толщиной стенки до 4 мм. Кроме того, для трубопроводов диаметром до 152 мм возможно применение газовой сварки (без разделки кромок - до 3 мм, и односторонним скосом кромок - до 5 мм).
Соединение разностенных труб на трассе допускается без дополнительной обработки кромок:
для толщин стенок не более 12,5 мм, если разность толщины не превышает 2 мм;
для толщин стенок свыше 12,5 мм, если разность толщины не превышает 3 мм. В этом случае смещение стыкуемых кромок не допускается.
Соединение труб или труб с запорной и распределительной арматурой с большей разностью толщин стенок осуществляют посредством вварки между стыкуемыми элементами переходников заводского изготовления или вставок из труб промежуточной толщины длиной не менее 250 мм.
Допускается выполнять непосредственную сборку и сварку труб или труб с деталями трубопроводов при разностенности до 1,5 толщин при специальной обработке, прилегающей к торцу поверхности более толстой трубы или детали (рис.2, а). Сварка захлесточных стыков разностенных труб не допускается.
Непосредственное соединение труб с запорной и распределительной арматурой разрешается при условии, если толщина стыкуемого торца арматуры не превышает 1,5 толщины стенки трубы с подготовкой патрубка арматуры согласно (рис. 2, б). Указанная подготовка должна быть осуществлена заводом-поставщиком.
Рис. 2. Подготовка для сварки торцов труб и деталей с разной толщиной стенки.
Требования к сборке труб
Сборка стыков труб должна гарантировать:
Перпендикулярность стыка к оси трубопровода. Отклонение от перпендикулярности не должно превышать 2 мм;
равномерность по периметру зазора, находящегося в пределах значений, регламентированных соответствующими стандартами и инструкциями;
минимально возможную величину смещения кромок, регистрируемую универсальными шаблонами, не превышающую допустимых значений (для магистральных трубопроводов - 0,2 толщины стенки, но не более 3 мм, для распределительных - (0,15 толщины стенки + 0,5 мм);
смешение продольных заводских швов относительно друг друга на расстояние не менее 100 мм - для труб диаметром более 100 мм и на 1/3 длины окружности - для труб диаметром менее 100 мм. В случае технической невозможности выполнения указанных требований назначается дополнительный ультразвуковой контроль сварочного соединения на данном участке стыка.
При изготовлении труб большого диаметра, корпусов цилиндров из обечаек применяют следующие виды сборки и сварки - "Сборка и сварка обечаек корпуса."
Предварительный подогрев
Предварительный подогрев является одной из важнейших технологических операций, позволяющих регулировать термический цикл сварки. Известно, что структура и свойства сварного соединения в значительной степени определяются скоростью охлаждения металла в интервале температур 800-500°С (наименьшей устойчивости аустенита). При высоких скоростях охлаждения возможно образование закалочных структур типа мартенсит в ЗТВ, обладающих высокой прочностью и низкой пластичностью, а также склонностью к образованию холодных трещин. Особенно это относится к низколегированным сталям с эквивалентом углерода 0,43% и выше. Эти стали весьма чувствительны к действию термического цикла, к концентраторам, а зона термического влияния склонна к охрупчиванию. Наиболее ярко эти явления проявляются при ручной дуговой сварке, когда скорость охлаждения металла ЗТВ может достигать 70°С/с. При заданной толщине стенки трубы регулировать скорость охлаждения зоны термического влияния можно изменяя начальную температуру стыкующих кромок предварительным подогревом. Особенно важно это при сварке корня шва электродами с целлюлозным покрытием, когда скорость охлаждения максимальна по сравнению со сваркой других слоев шва, уменьшена погонная энергия сварки (скорость сварки такими электродами вдвое превышает скорость сварки электродами с основным покрытием) и увеличена склонность и образованию холодных трещин за счет повышения содержания диффузионного водорода в металле шва. Предварительный подогрев не только уменьшает вероятность образования закалочных структур в ЗТВ, но и создает условия для активной эвакуации диффузионного водорода из металла шва и указанной зоны. Что, в свою очередь, повышает стойкость сварных соединений против образования холодных трещин, особенно при использовании электродов с целлюлозным покрытием, когда содержание водорода в шве может достигать 50 мм на 100 г наплавленного металла.
Температуру предварительного подогрева выбирают в зависимости от химсостава стали (по эквиваленту углерода), толщины станки трубы, температуры окружающего воздуха и вида электродного покрытия. Эти параметры, как правило, регламентируются соответствующими стандартами и технологическими инструкциями. Так, например, в СНГ руководствуются ВСН 066-89 (табл. 2). При сварке электродами с целлюлозным покрытием температура предварительного подогрева повышается на 75 °С.
Таблица 2
За рубежом часто при выборе подогрева оперируют показателем трещиностойкости сварных соединений, определяемый по формуле Ито-Беесио:
где: [Н] - содержание диффузионного водорода, мм/100 г;
t - толщина свариваемых пластин, мм. Температура подогрева определяется на эмпирической формуле:
(°С)ТП.П= 1440 Рcм - 392.
Предварительный и, при необходимости, сопутствующий подогрев следует осуществлять нагревательными устройствами (газовыми или электрическими), обеспечивающими равномерный нагрев металла по всему периметру свариваемого стыка. Ширина зоны разо¬грева труб в каждую сторону от шва должна быть не менее 75 мм.
Температуру предварительного и сопутствующего подогрева при соединении труб (или трубы с деталью) из различных марок стали или с различной толщиной стенки, которые должны быть нагреты на разные температуры, устанавливают по максимальному значению.
Технология и техника ручной дуговой сварки
Почти 60% объема сварочных работ при строительстве трубопроводов приходится на ручную дуговую сварку. Это соединение секций или отдельных труб в непрерывную нитку, сварка переходов через естественные и искусственные преграды, сварка захлестов, вварка катушек, крановых узлов, отводов и др.
Технология ручной дуговой сварки определяется прежде всего материалом труб, подлежащих сварке. В зависимости от марки стали трубы и условий эксплуатации выбирают сварочные материалы. После этого устанавливают технологию и технику сварки, а также схему организации работ, при этом руководствуются заданным темпом строительства трубопровода. При заданных сварочных материалах технология сварки зависит от диаметра и толщины стенки трубы.
Беспрекословным правилом при строительстве магистральных и распределительных трубопроводов есть требование к минимальному количеству слоев в шве. Для труб с толщиной стенки 6 мм и менее - 2 слоя, с толщиной стенки более 6 мм - 3 слоя.
Наиболее ответственным является корневой слой шва. Он должен надежно проплавлять кромки свариваемых труб и образовывать на внутренней поверхности шва равномерный обратный валик с усилением 1-3 мм. Допускается на отдельных участках стыка длиной не более 50 мм (на каждые 350 мм шва) ослабление корня шва (мениск) величиной до 10-15% от толщины стенки трубы. Наружная поверхность корневого слоя должна быть гладкой, мелкочешуйчатой и иметь плавное сопряжение с боковыми поверхностями разделки. Оптимальной формой наружной поверхности шва можно выполнять как шлифовальной машинкой, так и пневмомолотком в соответствии с требованиями инструкции.
При сварке труб диаметром 1020 мм и более после сварки корня шва рекомендуется выполнить подварку корневого слоя изнутри трубы в тех местах, где имеется не провар корня, и обязательно в нижней четверти периметра стыка (изнутри), т.е. на том участке, который при сварке корня шва снаружи выполнялся в потолочном положении. При ручной сварке корня шва поворотных стыков труб большого диаметра подварку выполняют по всему периметру стыка. Подеарочный шов обеспечивает провар корня, он должен иметь мелкочешуйчатую поверхность, плавно сопрягающуюся с внутренней поверхностью трубы без подрезов и других дефектов. Усиление подварочного шва должно составлять не менее 1 и не более 3 мм. Подварку выполняют электродами основного типа диаметром 3-4 мм.
Заполняющие слои шва надежно сплавляются между собой и проплавляют кромки свариваемых труб. После каждого слоя шва необходимо обязательно очищать поверхности шва от шлака.
Облицовочный шов имеет плавное очертание и сопряжение с поверхностью трубы, без подрезов и других видимых дефектов. Усиление шва должно быть не менее 1 и не более 3 мм. Ширина шва перекрывает ширину разделки на 2-3 мм в каждую сторону.
В конце смены сварной стык должен быть заварен полностью. Это требование вызвано тем, что трубопровод в течение суток претерпевает действие изменения температуры окружающего воздуха, которое особенно существенно при смене для ночью и ночи - днем. Изменение температуры вызывает возникновение в трубах и сварных стыках напряжений, которые могут быть весьма высокими.
Если стык заварен не полностью, то в ослабленном сечении шва напряжения могут превысить предел текучести и даже временное сопротивление разрушению металла шва и стык разрушится. Особенно опасна эта ситуация при отрицательных температурах воздуха, когда снижается пластичность металла.
В зависимости от типа рекомендуемых электродов существует 3 наиболее распространенных схемы сварки: сварка стыка электродами с основным покрытием, сварка стыка электродами газозащитного типа, сварка корня шва и горячего прохода электродами газозащитного типа, а заполняющих и облицовочного слоев - электродами с основным покрытием.
Сварку электродами с основным покрытием выполняют снизу вверх с поперечными колебаниями, амплитуда которых зависит от ширины разделки стыка. При поточно-расчлененном методе сварки каждый сварщик выполняет определенный участок шва, положение которого зависит от числа сварщиков, работающих одновременно на одном стыке. На трубах большого диаметра их число может достигать четырех. Как правило, если сварщиков двое, то они выполняют сварку снизу, от надира, и идут вверх по периметру в направлении (по циферблату часов) 6-3-12 и 6-9-12. При этом в потолочной части стыка замок следует смещать на 50-60 мм от нижней точки окружности трубы. В двух смежных слоях замки должны отстоять друг от друга не менее чем на 50-100 мм. Если сварщиков четверо, то первая пара варит участок стыка (по циферблату) 6-3 и 6-9, а вторая пара - 3-12 и 9-12.
Схема последовательности наложения двух слоев при сварке снизу вверх электродами с основным покрытием приведена на рис. 3, а. Все последующие нечетные слои выполняют по схеме первого слоя, все четные - по схеме второго слоя. Римские цифры показывают последовательность сварки отдельных участков шва. В зависимости от пространственного положения сварки рекомендуются значения тока, приведенные в табл.3.
При использовании электродов с покрытием основного вида следует применять только аттестованные для трубопроводного строительства марки электродов.
Таблица 3
При использовании электродов газозащитного типа сварку корня шва выполняют сверху вниз без колебательных движений, опираясь концом электрода на кромки свариваемых труб. Сварку выполняют постоянным током обратной или прямой полярности при напряжении холостого хода источника питания не менее 75В. Значения сварочного тока при сварке электродами диаметром 3,25 мм не должны превышать 100-110А; при сварке электродами диаметром 4 мм в нижнем и полувертикальном положении 120-160А, в остальных положениях 100-140А. Скорость сварки следует поддерживать в диапазоне 16-22 м/ч. Изменяя в процессе сварки угол наклона электрода от 40 до 90°, сварщик сохраняет образующееся при сквозном проплавлении кромок технологическое окно, через которое он наблюдает за оплавлением кромок.
Для снижения уровня остаточных сварочных напряжений в сварном соединении периметр неповоротного стыка разбивается на симметричные, диаметрально противоположные участки и многослойная сварка выполняется в последовательности, приведенной на рис. 4. Больший эффект снижения сварочных напряжений и деформации дает применение обратноступенчатого метода сварки и одновременное заполнение разделки двумя или четырьмя сварщиками.
При сварке трубопроводов небольшого диаметра (до 530 мм) с целью уменьшения объема монтажных работ в траншее часто практикуется укрупнение в секции труб сваркой с поворотом стыков на 90 или 180°. Трубу делят по окружности на четыре примерно одинаковых по длине участка. Заварив участки 1 и 2 стык поворачивают на 90° для сварки участков 3 и 4 (рис. 5). Затем, выполняя очередной поворот на 90°, производят последовательносварку участков 5 и 6, 7 и 8.
В другом случае, после сварки участков 1 и 2 (рис. 6) выполняют поворот стыкуемых труб на 180° для сварки участков 3 и 4. Затем поворот на 90° и 180° для сварки участков 5 и 6, 7 и 8 соответственно.
Рис.5 . Сварка с поворотом труб на 90°: а - первого слоя, б - второго, 1...8 - последовательность выполнения участков слоя.
Рис.6 . Сварка с поворотом труб на 180°: а - первого слоя, б - второго, 1...8 - последовательность выполнения участков слоя.
Успех такого сложного соединения во многом зависит от правильного выбора способа сварки труб , который выбирают для конкретного вида металла.
В целом же лучшим вариантом для соединения труб признаётся электродуговая сварка.
Но это под силу только сварщику, имеющему хотя бы минимальный опыт работы. Новичку желательно сначала потренироваться.
При работе с трубами из толстого металла лучше использовать непрерывный способ сварки при токе в 40-60 ампер. Важно именно проварить металл, а не прорезать его. При этом электрод ведётся не очень быстро – иначе качество шва пострадает.
Прерывистую точечную сварку труб применяют при сваривании тонкостенных труб. Здесь необходимо строго следить за процессом, потому, что стенки легко проварить насквозь. Для соединения тонких труб лучше использовать полуавтоматы. Они работают с малой силой тока, обеспечивая отличное качество как непрерывного, так и точечного сварного шва.
Профессионалы советуют при сварке труб ручной дуговой сваркой делать тройной шов – он будет надёжнее одиночного. Наиболее удобно работать сварщику с поворачиваемой трубой. Сварка так называемых поворотных стыков производится следующим образом:
- сначала соединяется одна четверть диаметра трубы;
- потом трубу поворачивают на 180 градусов, и варится противоположный первому шву участок;
- далее новый поворот и сварка второй четверти диаметра трубы;
- после этого производится ещё одно вращение трубы, и соединяется оставшейся участок.
После очистки от окалины на первый шов наносят второй. Заключительный третий шов начинают наносить с противоположной стороны второму шву.
При сварке жёстко зафиксированной трубы применяется иная методика:
- первый шов ведут снизу вверх до половины диаметра трубы, а потом опускается вниз, обратно к началу;
- нанесение второго шва начинают также снизу, но ведут с другой стороны и в обратном направлении.
Другие способы сварки
Подобный способ сварки неповоротных стыков исключает непроваренные участки, и шов получается более надёжным. При выполнении третьего шва работают по схеме первого варианта.
Самое надёжное соединение даёт многослойная сварка. В некоторых случаях применяют сварку спиралью – очистив от окалины начальный шов, второй ведут параллельно валику первого.
Сварка медных труб
Выбор способа сварки медных труб зависит от назначения соединяемых труб, герметичности шва и иных характеристик. Применяют три метода сварки – электродуговую, контактную и газовую.
Наиболее перспективной признаётся электродуговая сварка с использованием неплавящегося электрода из вольфрама и присадочной проволоки, в состав которой добавлены раскислители.
В качестве защитного газа целесообразно использовать азот, потому что сварка получается дешёвой.
Однако при работе с тонкостенными медными трубами лучше применять аргон.
Самой востребованной остаётся сварка стальных труб – как в производстве, так и в быту. Здесь существенную роль играет квалификация сварщика. Что касается сварочного оборудования, то используются электросварки, газосварки и полуавтоматы.
Перед началом сварки проводят предварительную тщательную очистку кромок от загрязнений и окислов, затем снимают фаску, что позволит получить V-образную площадь, благодаря которой шов станет прочным и герметичным.
При сварке газовой горелкой достаточно одного шва. С целью исключения непровара окончание шва немного накладывается на начало. Сорт присадочного материала должен быть одинаковым с металлом свариваемой трубы.
А самыми распространёнными на сегодня являются электросварка и полуавтоматическая. В обоих случаях процесс начинается с подготовки свариваемых труб. Затем соединяемые части центрируют и равномерно прихватывают в трёх-четырёх точках.
Первый шов «тройкой». Важно заполнить фаску по высоте всего на две трети. После очистки шва от шлака и проверки качества работы, меняют электрод «четвёрку» и приступают к нанесению дополнительного шва.
Сварка оцинкованных труб
Специальная технология сварки оцинкованных труб позволяет соединять их, не нарушая цинкового покрытия. На место стыковки наносят флюс, который и обеспечивает защиту от выгорания покрытия. Под флюсовым слоем цинк сначала от воздействия тепла становится вязко-жидким, затем расплавляется, но не выгорает и не испаряется. По завершению сварки это обеспечивает защиту от коррозии.
При работе с оцинкованным материалом крайне важно наличие вентиляции. В противном случае от цинковых паров сварщик может «заработать» лёгочное заболевание или хуже того, задохнуться.
Сварка профильных труб
Основной способ сварки профильных труб – обычное соединение торцов встык. Выполняют её дуговым или газовым методом, но благодаря простоте и качественному шву больше распространён первый из них. Однако электросварка профильной трубы требует опыта работы сварщика, хотя бы небольшого.
Много зависит, к примеру, от правильного подбора электрода. Чем он толще, тем мощнее дуга. Излишне толстым электродом профильную трубу можно прожечь, а слишком тонким получить непрочный шов. Учитывая то, что для данного изделия характерная толщина составляет 1,5-5 мм, подойдут «двойка и «тройка».
При работе с профильными трубами важна скорость движения электрода по материалу. Если замедлиться, то есть риск прожечь деталь, при убыстрении – получить некачественный шов. Оптимальное движение подбирается опытным путём.
Настоящего профессионализма требует сварка газовых труб , которая довольно опасна. Работать нужно быстро и качественно.
Перед началом соединения обрабатывают кромки труб: очищают от загрязнений. Если труба толстостенная – больше 4 мм, то производят скос кромок для облегчения прогревания металла на месте контакта.
Практикуются два способа сварки газовых труб:
- сварка слева направо. Применяют тогда, когда толщина металла больше 5-ти мм. Дуга направляется на уже приваренный участок, вместе с горелкой перемещается присадка. Вариант экономит расход газа и повышает производительность на 25%;
- сварка справа налево. Здесь горелку продвигают по не приваренным участкам – присадочная проволока «идёт впереди паровоза». Лучший метод для работы с тонкостенными газовыми трубами.
Способ электродуговой сварки трубопроводов часто применяют при монтаже или изготовлении технологических линий. Производятся они на постоянном или переменном токе.
Экономичным, а значит, более выгодным является сварка на переменном токе, потому что получается меньший расход энергии. Да и оборудование требуется более доступное.
Наиболее распространенный метод монтажа инженерных сетей — сварка труб электросваркой.
Сварка труб – процесс достаточно простой. Надо только тщательно соблюдать этапы и технику выполнения этой работы.
Стальные детали
1.Входной контроль
Труб начинается с проверки на соответствие трубы нормативным требованиям.
Что проверять:
- Наличие сертификата соответствия.
- Маркировку.
- Эквивалент углерода. Эта величина говорит о свариваемости стали. В зависимости от содержания углерода выбирается технология сварки труб.
- Длину детали.
- Диаметр детали и толщину стенки.
- Толщину стенки.
- Овальность концов детали.
- Кривизну детали.
- Наличие повреждений и дефектов на поверхности металла.
2.Подготовка стыков к свариванию
Подготовка стыков выполняется механической обработкой или термической резкой. Если использовалась термическая резка, то полученную кромку необходимо обработать абразивным инструментом, либо резцом.
Если вы планируете варить трубу из низколегированной или углеродистой стали без использования подкладного кольца, фаску выполняйте только механическим путем. Точно также разделывается кромка на трубах из легированных и высоколегированных сталей (в том числе, из нержавеющей стали).
Подготовленная кромка не должна иметь острых углов, заусенцев, вырывов и резких переходов. Все эти « излишества» тщательно зачищаются напильником или абразивным кругом.
Для контроля качества обработки кромок сварщики пользуются шаблонами проверки:
- углов;
- превышения кромок;
- притупления кромок;
- зазора в нахлесточном соединении;
- зазора в тавровом соединении;
- зазора в стыковом соединении.
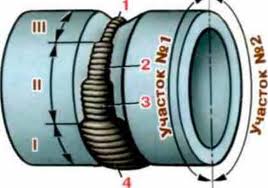
3. Выбор технологии сваривания труб.
Электросварка труб в основном выполняется двумя способами:
- покрытым электродом;
- ручная неплавящимся электродом.
Первый способ применяется для углеродистых сталей, второй – для легированных (нержавеющих в том числе).
4.Как варить трубы электросваркой покрытым электродом.
1.Режимы:
- Род и полярность тока зависит от толщины стенки трубы, марки стали и марки покрытого электрода.
- Сварочный ток определяется толщиной электрода. Чтобы его рассчитать, надо диаметр электрода умножить на (30-40). Полученное число будет равняться сварочному току в амперах.
- Напряжение на дуге определяется ее дугой. Оптимальная длина дуги находится в диапазоне от половины диаметра электрода до полного диаметра электрода плюс 1.
- Скорость сварки сварщик выбирает в зависимости от геометрических размеров .
Сейчас в сети Интернет можно найти таблицы зависимостей всех перечисленных величин. Кроме того, там можно найти множество обучающих материалов, в которых подробно освещена электросварка труб: видео, инструкции, рекомендации.
2.Сборка стыков труб малого диаметра (до 100 мм) при толщине стенки от 2 до 10 мм из низкоуглеродистых сталей:
- Cтыки собирают в приспособлениях и прихватывают в одной или двух . Если точек прихвата две, то они располагаются симметрично.
- Стыки, скрепленные одной прихваткой, обваривают сразу, начиная со стороны, противоположной прихватке;
- Если толщина стенки меньше 3 мм, прихватку выполняют электродом диаметром не более 2,5 мм;
- Стыки изделия с толщиной стенки более 4 мм сваривают не менее, чем в два слоя – корневым швом и облицовочным валиком.
- При сварке деталей диаметром от 30 до 83 мм вертикальный стык сваривается участками по ¾ периметра;
- Каждый последующий валик горизонтального стыка укладывается в противоположном направлении;
- «замковые» участки последующих валиков смещают относительно предыдущих швов.
3.Поворотные стыки:
- При сварке стыков во вращателях скорость вращения изделия должна равняться скорости сварки.
- Положение сварочной ванны, наиболее удобное для формирования шва, находится не в самой верхней точке стыка, а в точке, отстоящей от вертикали на 30-35 градусов в сторону, противоположную вращению.
- Если применение вращателей нецелесообразно или их нет, свариваемые стыки надо поворачивать на углы 60-110 градусов. Благодаря этому, шов формируется в самом удобном, нижнем положении.
- трубы с поворотом на 180 градусов сваривают в три приема:
- сначала в два приема сваривают две верхние четверти диаметра трубы в направлении навстречу друг другу одни или двумя слоями;
- затем переворачивают трубу на 180 градусов и сваривают оставшуюся часть стыка на всю толщину;
- затем трубу еще раз поворачивают на 180 градусов и проваривают оставшуюся разделку.
4. Сварка неповоротных стыков:
- Вертикальные неповоротные стыки варятся в два приема. Периметр стыка условно делится вертикальной осевой линией на два участка. Каждый из них имеет три положения: потолочное, горизонтальное и нижнее. Потолочным называется участок, занимающий примерно 20 градусов от самой нижней точки детали.
Нижним положением – участок, занимающий тоже примерно 20 градусов от верхней точки детали. Между этими положениями располагается горизонтальное положение. Сварка начинается с потолочного положения и заканчивается нижним (т. е. ведется с крайней нижней точки детали к крайней верхней).
Каждый участок варится короткой дугой, равной половине диаметра электрода. Перекрытие швов (замок) зависит от диаметра детали и может составлять от 20 до 40 мм. Начинать сварку надо «углом назад», а заканчивать «углом вперед».
- Горизонтальные неповоротные стыки варятся «углом назад». Наклон электрода относительно вертикальной оси должен составлять 80-90 градусов. Варить надо средней дугой.
5.Сварка труб электросваркой в защитных газах: аргонодуговая сварка.
Режимы:
- Сварочный ток зависит при сварке за один проход от толщины стенки детали, а при многопроходной – от высоты валика. На каждый мм диаметра электрода назначается 30-35 А.
- Напряжение на дуге держат минимальным, что соответствует сварке короткой дугой.
- Скорость сварки регулируется так, чтобы гарантировалось проплавление кромок и формирование размеров шва.
- Расход аргона зависит от марки стали, режима сварочного тока и находится в диапазоне от 8 до 14 л/мин.
- Варить сплошной шов надо сразу после установки прихваток, которые при выполнении первого слоя следует переплавлять.
- Подача аргона прекращается только через 5-8 секунд после обрыва дуги.
6.Контроль качества сварного шва.
- Самый распространенный метод контроля сварки – внешний осмотр. В процессе осмотра выявляют наличие трещин, прожогов, подрезов, непроваров и пр.
- Перед началом осмотра сварные швы должны быть очищены от шлака. Осмотру подвергаются все швы без исключения.
- Для проверки геометрических параметров швов используются шаблоны, щупы, стандартные измерительные инструменты.
- Герметичность швов проверяется водой (гидравлическое испытание) или газом (пневматическое испытание).
7.Техника безопасности.
При выполнении сварки возможны травмы такого рода, поражение электрическим током, ожоги расплавленным металлом, ожоги глаз лучистым излучением. Чтобы этого не произошло, необходимо:
- надежно изолировать все токоведущие части;
- заземлить корпуса источников питания, вспомогательное оборудование. Сечение заземляющих проводов должно быть равным или более 25 кв. мм.
- спецодежда и рукавицы должны быть сухими;
- в тесных помещениях следует использовать резиновые коврики и галоши;
- не приступать к работе без защитного щитка, размеры которого полностью закрывают голову и лицо сварщика.
8. Сварка труб электросваркой: цена.
Стоимость сварки труб зависит от диаметра и материала детали. Так, например, один см стыка трубы Ду15 стоит 25 рублей, а Ду50 – 22 рубля.
При сборке горизонтальных стыков труб под сварку, на нижней трубе не обязательно выполнять полную разделку кромок. Допускается сделать лишь небольшую разделку, величиной 10°. Данный приём улучшает процесс сварки металла, при этом, не снижая её качества (см. схему а) на рисунке ниже). При подготовке не ответственных трубопроводов к сварке, кромку на нижней трубе зачастую, совсем не разделывают (см. схему б) на рисунке ниже).
Наиболее хорошие результаты получаются при сварке горизонтальных стыков труб отдельными узкими слоями. Первым валиком проваривают корень шва (см. схему в) на рисунке ниже), для этого применяют электроды диаметром 4мм. Силу тока устанавливают в пределах 160-190А. Электроду сообщается возвратно-поступательное движение, при этом, на внутренней стороне стыка должен образоваться нитевидный валик, высотой 1-1,5мм.
После наложения первого слоя, его поверхность необходимо тщательно зачистить. Второй слой выполняют с тем учётом, чтобы он перекрывал первый слой при возвратно-поступательном движении электрода и при его небольшом колебании от края нижней кромки до края верхней кромки. Сварка второго слоя производится в том же направлении, что и сварка первого слоя.
После выполнения второго слоя, силу сварочного тока увеличивают до 250-300А и выполняют третий слой. Сварку ведут электродами диаметром 5мм, это позволяет увеличить производительность процесса сварки. Наплавление третьего слоя должно происходить в направлении, противоположном наплавлению сварки первых двух слоёв. Третий валик должен перекрывать 2/3 ширины второго валика. Наплавление четвёртого валика происходит в том же направлении, но располагаться он должен в углублении третьим валиком и верхней кромкой.
При сварке горизонтальных стыков труб более, чем в три слоя, каждый последующий слой, начиная с третьего, должен выполняться в направлении, противоположном предыдущему. Трубы, диаметр которых не превышает 200мм, обычно сваривают сплошными швами. Если же диаметр свариваемой трубы превышает 200мм, то сварку выполняют обратно-ступенчатым способом.
Видео: сварка труб с горизонтальным стыком